TOP FOUR BENEFITS OF AUTOMATED TUBE BENDING
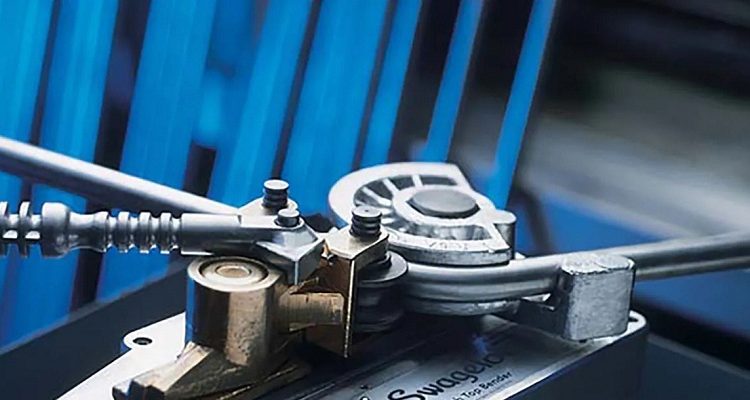
The market for metal pipes and tubes is expected to reach $14.5 billion in the US alone by 2023, according to IBIS World. That research shows the period from 2018 to 2023 declined slightly in demand, but 2023 should return the industry to more than 1 per cent growth per year.
Metal tubes are an essential part of the global economy. They’re instrumental in fabricating everything from cars and trucks to bridge components, airplanes and musical instruments. Bending metal tubes is one way to increase their usefulness and tailor them to specific applications.
The bending process is historically a labour-intensive one fraught with potential errors and safety issues. Automating this task could deliver considerable added value, money saved, more consistent results and a more efficient machine shop or manufacturing plant. Here are several benefits of automated tube bending worth knowing.
1. Readies organisations for emerging marketsThere are several sources of ongoing pressure throughout the automotive industry. One is the call to drive costs down however possible — another concerns the unique manufacturing requirements of electric and hydrogen-powered vehicles and similar next-generation engineering designs. Electrification is a major step toward a smart, resilient power grid and cleaner commutes for employees and freight.
The process of manufacturing electric vehicles simultaneously exemplifies several of these challenges. EVs require fast processing for challenging or unconventionally shaped raw materials. For example, many need tubes bent into shapes other than circles. The lightweight materials necessary to preserve the vehicles’ range can be more challenging to work with than conventional materials and fabrication techniques.
Automated tube bending makes manufacturing these elements easier, faster and more error-free to achieve even while overall EV manufacturing ramps up to meet quickly ballooning demand. The race to get affordable, lightweight, long-range EVs to market is heating up. Manufacturers specialising in high-speed, high-accuracy automated tube bending will position themselves as an ally to this emerging market.
2. Makes existing processes more efficientThe best way to understand the practical benefits of adopting automated tube bending equipment is through a before-and-after comparison. One example saw Kawasaki bringing online tube-bending robots to increase efficiency and productivity with compelling results. The robot — called Bender Bot 1 — added considerable value to the process of manufacturing frames for ATVs and other four-wheeled vehicles.
Before:
- Machine attendants had to lift heavy tubes twice to bend them.
- The processes required unergonomic and potentially unsafe motions and placements.
- Efficiency and productivity were adequate but needed improvement.
After:
- Only one lift is required after robotic process automation.
- Human workers are free to pursue higher-value or more creative work.
- Kawasaki saw throughput rise to 700 tubes per hour by automating 33% of its bending-related processes.
Each of these improvements adds up to an industrial manufacturing process that’s faster and more accurate. At Lockheed Martin, turning to assembly-line automation for producing the F-35 Lightning II brought a 34-hour decrease in the time required to manufacture key fuselage components. Automation removes human inefficiency and redirects that talent toward more rewarding, less rote pursuits.
3. Makes machine shops safer and more transparent Automated tube bending tools are like other advanced machining equipment. They provide accurate and repeatable results every time with a substantially reduced need for human attendants or active intervention.
Working with heavy metal components isn’t the safest line of work, but automation can take vulnerable flesh and bones out of the fray. One advanced machine control system sees equipment functioning without manual adjustments for 60–80 hours at a time.
Maintaining safety is just one moral obligation in manufacturing plants and machine shops — transparency and process ownership are others. Consider the process of chamfering metal pipes. With advanced automation and machine vision, sensors embedded in the equipment can carry out automatic 360° inspections of each task as it completes. This yields lots of valuable information, including:
- The condition of the workpiece before work begins.
- Whether and when workers carried out specific tasks.
- Which machine or production line was responsible for the work.
- How long the process took and the level of accuracy achieved.
Verifying that work has been done reduces lost time, the need for rework and the likelihood of compounded errors. Some high-stakes industries — like aerospace, automotive and health care manufacturing — even require or strongly encourage verifications at multiple stages of fabrication. Automation will make this part of the job painless to carry out, verify and document.
4. Expands the possibilities of mass customisationProduction flexibility is one of the most valuable qualities an industrial manufacturer can possess today. For a start, the pressures of the pandemic caused many businesses to prioritize different products or business models as demand for their products and others changed dramatically in real-time. People probably haven’t seen the last of distilleries pivoting to making hand sanitizer in a pinch.
This kind of adaptability isn’t just a requirement during a public health crisis. Adjusting production lines quickly is also vital for achieving mass customization — a key feature of Industry 4.0.
Electrified and automated bending and other industrial equipment can reprogram and adapt faster than conventional machines. With these tools, variables like mandrel position and the pressure and position of the dies don’t require manual intervention to fine-tune during changeovers. The resulting ability to create customized products or parts at scale and the nimbleness to switch to fabricating something else quickly without fully resetting or building an entirely new production line will boost competitiveness and earning potential.
Automated tube bending: Safety, productivity and efficiency enhancedManufacturers must recognise the benefits of automation across industries and disciplines. The most successful automation transitions begin with a specific challenge to solve, so look over operations to find places where safety, productivity and efficiency may be flagging. Automating those processes could unlock competitive and innovation potential leaders didn’t know their organisation had.